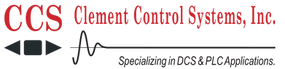
PROJECTS
We’ll provide detailed resumes of all our staff upon request, but here’s a brief review of some typical projects that our personnel have either completed or are currently involved with:
​
-
DELTA V DCS Upgrade Project – Valero Oil, Meraux Refinery | Involved with the development of DCS points, graphics, and serial interfaces between Delta V and various SIS systems, PLC, and other devices. Responsible for developing the construction packages for the entire refinery DCS upgrade project. Other duties include the review and support of design efforts on projects currently being developed to ensure that drawing packages conform to Valero standards. Participated in commissioning (Hot Swap Over) of the DCS and of 6 existing Triconex SIS systems.
-
Marine Terminal MOL-A Upgrades – LOOP, LLC | The project replaced a Square D PLC with an Allen-Bradley ControlLogix PLC for the control of a 7000 HP Diesel Engine and Pump. Performed all Control System design and engineering, programming, HMI development, FAT and SAT Testing.
-
Tank Farm Storage Tanks Project – LOOP LLC | Responsible for the PLC based control system and safety system design and implementation for a 7.2 MM barrel tank storage facility and supporting transfer pumps. Safety system responsibilities included the design, analysis, and justification of the SIS system and development of all DOT Safecharts. The PLC was a Modicon Quantum with WonderWare HMI graphics.
-
Oily Water Treatment Skid – Pemex | Oily Water Treatment Skid that included an Inducted Gas Floatation Cell, Horizontal Water Skimmer, Corrugated Plate Interceptor, Chemical Injection, and Solids Filter. Designed all I&E circuits for local PLC control of the skid. Specified all instrumentation and electrical equipment. Created the Field Construction Package consisting of wiring diagrams, loop drawings, instrument location plans, fabrication drawings, assembly drawings, standard installation details, routing plot plans, cable schedules, and the Scope of Work.
-
Caverns Control System Upgrade Project – LOOP, LLC | Responsible for the PLC based control system and safety system design and implementation for a 5-million-barrel crude oil cavern storage facility. Safety system responsibilities included the design, analysis, and justification of the SIS system and development of all DOT Safecharts. The PLC was a Modicon Quantum with WonderWare HMI graphics.
-
Coke Handling System – Marathon Ashland, LLC | Responsible for the control systems efforts for a 2-mile $24MM conveyor system to transport coke from the plant’s coker unit to a barge loadout facility on the river. Used Siemens TI series 505 PLC’s with 555 processors and remote I/O racks. Used WonderWare HMI.
-
Leak Detection Project – LOOP, LLC | The purpose of this project was to use filtering equations on flow measurements monitored by the Square D PLC’s in order to eliminate the “noise” associated with the analog measurements. The equations provided more accuracy that made leaks easier to detect.
-
Webster Blowdown Project – ExxonMobil Friendswood Gas Field | A dehydration plant and gas separators were installed at the Friendswood gas field controlled by Modicon PLC’s and Bristol-Babcock Teleflow flow computers. Personal computers in the field office, running Intellution FIX32 software, were used as the operator interface. Responsibility was to program the PLC’s, the Intellution graphics, Intellution database and establish communication using a serial link broadcast over frequency hopping spread spectrum radios.
-
Marine Vapor Recovery HMI Upgrade – Murphy Oil USA | Completed the installation of an upgraded HMI for the MVR unit which is controlled by a GE 90-70. GE Cimplicity HMI was installed to replace an existing panel, and to provide for enhanced operability.
-
Chinook Main Pass Off-Shore Project – Mobil Oil | Responsible for the design and development of the PLC based control system consisting of multiple GE 90/70 and 90/30 PLC’s using Genius Block I/O modules and remote scanner I/O frames. The HMI is WonderWare 7.0.
-
CCR Reformer Upgrade Project – Mobil Oil | Responsible for the generation of graphics on the Honeywell TDC-3000 US stations and reorganizing the historization for existing database points related to the project.
-
Nitrogen Generator Project – WITCO, Gretna, LA | The scope was to install a new 400 hp nitrogen generator to meet the plant’s future demands. Also included in the scope was the design and installation of a new 2000 KVA substation. Engineering duties included equipment specifications, transformer and switchgear design, protective relay coordination, fault current calculations, motor starting analysis, and load flow studies.
-
Blending and Shipping Automation Project – Chevron Chemical Company | Designed and installed a 4000 I/O point Bailey F&P System 6 DCS for complete, integrated control of all B&S functions. Duties included all project management responsibilities in addition to the hands-on development of all data points, CCL programming, graphic configuration, DCS testing/startup.
-
OLOA 219 Centrifuge Project – Chevron Chemical Company | Responsible for the specification, CL programming, HPM database configuration, and GUS graphic generation for a centrifuge filtering system consisting of 2 high speed centrifuges and one scroll decanter, all controlled by a Honeywell TPS system.
-
LOCAP No. 6 Pump Reactivation Project – LOOP, LLC | Generated permissive and shutdown logic for a 13.8 kV pipeline booster pump and related lube oil system using Square D PLC’s. Interfaced the PLC to a field mounted operator interface and to the customer's existing SCADA system.
-
Viosca Knoll 340 Offshore Platform Project – Chevron USA | Responsibilities included network, system integration, safety system design, graphic development using WonderWare 7.1, and all PLC programming using Cimplicity Control 90 on GE’s 90/30 PLC’s.
-
Viosca Knoll 734 Offshore Platform Project – Exxon Mobil | Responsibilities included network design, system integration, safety system design, graphic development using WonderWare 7.0, and all PLC programming using Cimplicity Control 90 on GE’s 90/70 and 90/30 PLC’s. Remote I/O was utilized via GE’s Genius Blocks and Scanner I/O.
-
Continuous Area Upgrade Project – Chevron Chemical Company | Replacement of an existing Taylor MOD3 DCS and a Foxboro Micro-Blentrol system with Honeywell’s TPS DCS system. Project responsibilities include defining the scope of automation, managing the installation of all Honeywell hardware, and developing the DCS network configuration, CL programming, HPM data points, trends, reports, group displays, history groups, and GUS graphics.
-
Pulpmill Modernization Project – Westvaco Corporation | Installation of a Foxboro IA Series Distributed Control System and two control panels. DBASE IV and AutoLisp programs were developed and implemented to produce control loop diagrams with more accuracy and efficiency.
-
Honeywell TPS Implementation Team – Chevron Chemical Company | Responsibilities included designing the network topology and various interfaces, developing plans for migrating all manufacturing areas of the plant to one control system, bandwidth loading analysis, standardization of data points and DCS related graphics, and creating a GUS symbol library.
-
Power Boilers Control Systems Upgrade Project – Champion International Corporation | Responsibilities included specification and implementation of a Bailey Net 90 DCS for two multi-fuel power boilers, instrument specifications, and the design of SAMA control logic drawings.
-
Steam Plant DCS Upgrade Project – Vista Chemical Company | Responsible for the new ABB Mod 300 DCS used to control three boilers and the plant utilities unit. Configured all control logic for the project using a stand-alone ABB Mod 300 DPSS Turbo Node.
-
FCC Modernization Project – Chevron Company, U.S.A. | Designed and specified a Honeywell TDC 3000 DCS that would control the new Fluidized Catalytic Cracking Unit. The system included approximately 1200 I/O points and 800 loops and utilized five Advanced Process Managers. Configured the entire system using Honeywell’s “Workbook” database program. Wrote Control Language (CL) programs for control of the catalyst addition system and the back-up fluffing air system. Developed interfaces for several third-party systems on the Honeywell DCS such as Bentley-Nevada vibration monitor, Compressor Controls anti-surge controllers, and Triconex ESD system.
-
Temperature Data Collection – Murphy Oil Refinery | Murphy Oil uses panel mounted Westronics temperature indicators connected to multiplexors in the field to monitor temperatures in their refinery. The data was being recorded manually and entered into their Plant Information (PI) system. Wrote a Visual Basic application that would communicate with the Westronics indicators via an RS-232 serial link and automatically log data into the PI system. An interface screen was provided that would allow the operators to select the intervals at which the data was collected and also allowed them to monitor the status of the communication.
-
MTBE/TAME Offsites Project – Star Enterprise LOUP | Revised the configuration in the existing blend control system (Fischer & Porter DCU and Intermetrics Tank Gauging System) for the addition of new blend pumps and control valves.
-
HTU3 Project – Star Enterprise LOUP | Responsible for configuration of the Honeywell TDC 3000 DCS. This effort included not only the control database but also the network configuration (NCF) and History Module configuration as well. Wrote several CL programs for the Application Module and the Advanced Process Managers that controlled compressor loading and performed flow compensation calculations based on inputs from gas chromatograph analyzer (Applied Automation) inputs. Also programmed the ladder logic configuration for the area gas monitor PLC (Texas Instruments 545) and established the communication interfaces between the various monitors, analyzers, and ESD system.
-
Yokogawa DCS Upgrade Project – Murphy Oil Refinery | Involved with the development of DCS points, graphics, and serial interfaces between a Yokogawa CS3000 and various SIS systems, PLC, and other devices. Responsible for managing the safe construction of various DCS upgrade projects. Other duties include the review and support of design efforts on projects currently being developed to ensure that drawing packages conform to Murphy standards. Participated in commissioning of 3 new Triconex SIS systems.
-
Co-Generation Project – Chevron Chemical Company | $25 MM Co-Generation Project. The project involves the installation of a 25 MW electrical and steam generation facility using five natural gas turbines. Responsible for the overall project and all disciplines. Control system duties included the networking of the facility’s Allen Bradley Series 5 PLC’s and Square D PowerLogic meters to the plant’s existing Honeywell DCS-TPS.
-
13.8kV Upgrade Project – Chevron Chemical Company | Project Management on the 13.8 kV Upgrade Project whose scope was to increase the plant’s existing electrical distribution system to 14 MW to meet future load requirements. Responsibilities included the overall supervision, planning, coordination, documentation, and implementation of the project.
-
Blending and Shipping Area Pennzoil Upgrade Project – Chevron Chemical Company | Responsibilities included all software upgrades on the B&S Area’s Bailey F&P DCS system to accommodate new Pennzoil blends. Upgrades included new blend streams, a homogenizer pump, additional tank car and truck load spots, and a new zinc header.
-
Alumina Spray Dryer Project – Vista Chemical Company | The project required the expansion of the existing distributed control and emergency shutdown systems (ABB and Triconex) and the development of a detailed plant control philosophy from which the DCS and ESD programming were based.
-
Acetylene Plant VOC Reduction Project Phase 1 – Borden Chemical | Configured the Fisher-Rosemount Delta V DCS and designed the operator graphics. This DCS is a PC, Microsoft NT based system using OLE for configuration programming.
-
Styrene Expansion Project – Chevron Chemical Company | Responsible for existing plant upgrades to electronic instrumentation and a Honeywell TDC-3000 distributed control system.
-
Daphne Unit ESD Upgrade Project – Rhone-Poulenc Inc. | Configured the new Triconex ESD, Version 8 system under the rules of the French developed, Trivalex supervisory program. The Trivalex program provides an operator interface for the ESD system and has very strict rules governing the programming of the Triconex that give the interface its flexibility.
-
Y2K Project – Murphy Oil USA, Meraux Refinery | Conducted a Y2K analysis on Murphy Oil’s existing Honeywell TDC-2000, TDC-3000, and PLC-600 systems. Corrected all Y2K non-compliance items and performed system date tests.
-
Utilities Area Upgrade Project – Chevron Chemical Company | Upgrade of an existing gas fired oil heater, installation of a gas turbine, automation of existing batch reactors, and the automation of an existing blending unit. These processes are controlled with Siemens 545 and 565 PLC’s. TISTAR graphics and Lookout applications serve as operator interfaces.
-
Networking Project – Johnston’s of Chalmette | Designed and installed an ethernet fiber optic data highway to link all plant PC’s for data collection and reporting efforts. Also designed an RS-485 data highway to link together all plant Toshiba T2E PLC’s.